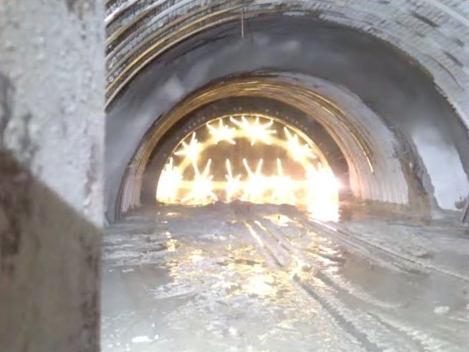
INGENIO web” del 20 Agosto 2020, Imready Srl – RSM
Premessa
Nel mondo delle costruzioni sotterranee, esistono due metodi principali per lo scavo di gallerie nella roccia: metodi di scavo convenzionali e metodi di scavo meccanizzati. Il primo include la potente tecnica Drill & Blast, mentre il secondo è meglio conosciuto per gli scavi eseguiti con enormi macchine denominate Tunnel Boring Machines (TBM).
C’è da dire però, che da circa un decennio il metodo di scavo drill & blast è passato ad essere considerato non convenzionale prendendo il posto che prima aveva lo scavo meccanizzato mediante TBM. Oggigiorno infatti, è molto frequente la realizzazione di tunnel mediante mezzi meccanici, specialmente in ambito urbano, riservando al metodo drill & blast speciali occasioni in cui non si può procedere all’apertura di un tunnel in maniera “convenzionale”.
Limiti di applicazione del metodo drill & blast
Il metodo può essere utilizzato in tutti i tipi di rocce e rispetto al metodo meccanico con TBM, il costo di iniziale di esecuzione del tunnel risulta essere generalmente inferiore.
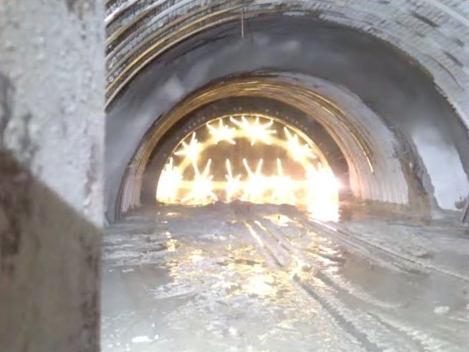
Per contro, dal punto di vista della produzione giornaliera, ovvero nell’avanzamento alla costruzione, il metodo presenta una produzione inferiore rispetto ad uno scavo eseguito con macchina TBM. Un ruolo importante lo occupa anche la lunghezza del tunnel nella scelta del metodo di scavo visti i costi onerosi di impianto cantiere e della macchina TBM stessa che ne scoraggiano l’utilizzo per tunnel di lunghezza inferiore ai 2 km. Di norma, per scavi di lunghezza superiore a 4÷5 km si utilizza spesso una TBM, mentre per lunghezze non superiori a 1,5 km, la tecnica Drill & Blast è generalmente la scelta migliore (sempreché non possano essere impiegate tecnologie alternative).
Prevedendo l’uso di esplosivo per l’apertura del cavo, il drill & blast comporta un’importante limitazione alla sua applicazione che è data dai livelli di vibrazione generati. L’energia sviluppatasi con il brillamento delle mine produce per buona parte lavoro che si traduce in frantumazione della roccia e relativo spostamento dal proprio sito. Solo una parte dell’energia viene trasformata in onde sismiche che si propagano nel terreno, radialmente ed a forte velocità, (2000÷5000 m/sec) provocando un’oscillazione del terreno stesso, che viene chiamata vibrazione, la cui intensità dipende direttamente dalla quantità di esplosivo fatta brillare.
Allontanandosi dalla zona di esplosione la velocità di oscillazione delle particelle, attorno alla posizione di equilibrio, tende a diminuire. In pratica, dunque, si genera nell’ambiente circostante il foro da mina un fenomeno assimilabile, in grandi linee, ad un terremoto naturale dal quale si differenzia per la più elevata frequenza delle vibrazioni e per la minor ampiezza delle oscillazioni. Sono stati fatti molti studi per individuare i vari parametri, che possono meglio caratterizzare le onde sismiche, al fine di valutare la loro attitudine a produrre danni. Anche gli studi condotti personalmente sul fenomeno delle vibrazioni indotte sulle strutture (Chiarelli 2004), hanno evidenziato che la velocità di vibrazione, associata alla frequenza, sia il parametro che meglio si adatta allo scopo. Altri colleghi considerano, invece, valida l’associazione di accelerazione e frequenza in particolare quando si vuol tenere conto non solo della quantità di energia trasmessa ma anche dal modo in cui essa è trasmessa.
È stato osservato che per distanze limitate, qualche decina di metri, le frequenze di vibrazioni trasmesse sono notevolmente maggiori nelle rocce rispetto alle terre. Le ampiezze di oscillazione, invece, misurate nelle terre, sono 2÷3 volte superiori a quelle misurate nelle rocce.
Le rocce compatte si comportano quasi elasticamente, assorbono meglio energia e trasmettono vibrazioni di frequenze ben maggiori, dell’ordine di 20÷80 Hz, che non i terreni sciolti, dove difficilmente si superano i 10 Hz.
È da notare che la frequenza tende, comunque, a diminuire col crescere della distanza dal punto di scoppio.
La presenza di fratture, faglie o stratificazioni può rinforzare, in direzioni preferenziali, le ampiezze di certe componenti delle vibrazioni trasmesse ed inoltre può dar luogo a interferenze, riflessioni di onda, complicando notevolmente il fenomeno dello smorzamento naturale da parte del terreno.
Ne consegue che nella roccia, in genere, si possono far esplodere cariche di esplosivo maggiori che non nel terreno sciolto senza danni dovuti alle vibrazioni.
La velocità è, comunque, la grandezza più comunemente adottata ai fini delle correlazioni con gli effetti dinamici delle vibrazioni.
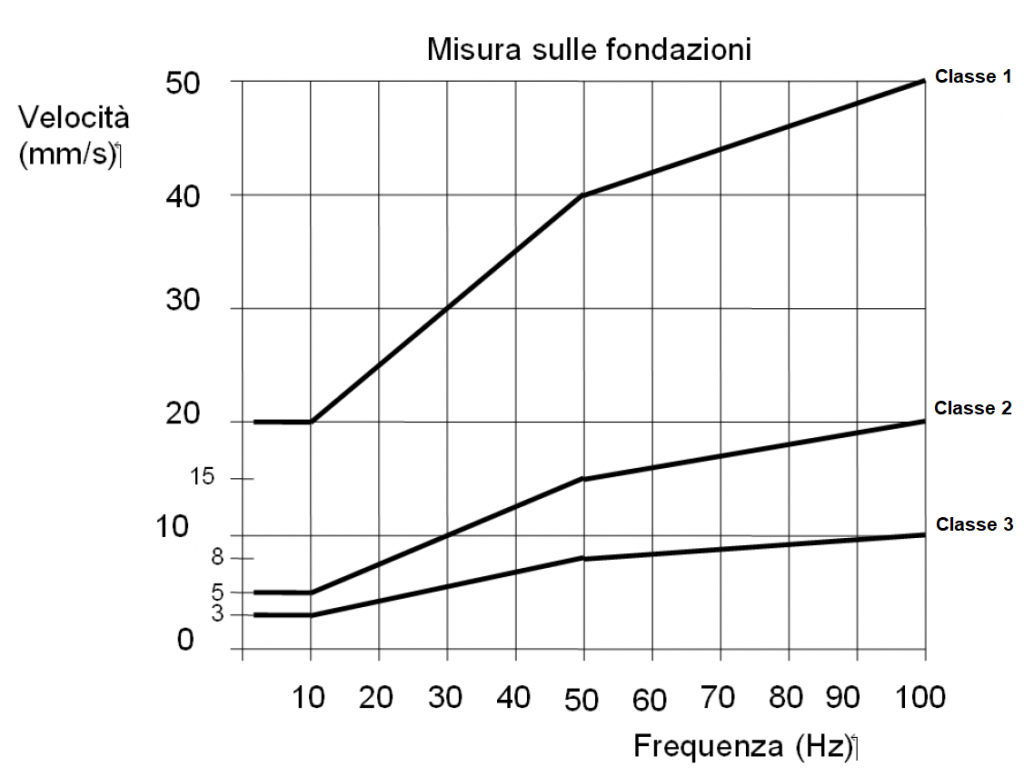
Nel grafico in figura 2 sono riportati i valori di riferimento per la velocità di vibrazione per campi di frequenza 1 – 100 Hz ammissibili sulle fondamenta degli edifici in base alla classe di costruzione secondo la normativa UNI 9916 : 2004.
Nel grafico di figura 2 le classi indicano rispettivamente:
Classe 1 – Costruzioni industriali, edifici industriali e costruzioni strutturalmente simili;
Classe 2 – Edifici residenziali e costruzioni simili;
Classe 3 – Costruzioni che non ricadono nelle classi 1 e 2 e che sono degne di essere tutelate.
L’esperienza mostra che i limiti riportati nel grafico precedente, siano da considerarsi validi per la tutela della stabilità degli edifici ma che siano troppo elevati per garantire gli edifici da qualsiasi danno in particolare arrecato agli intonaci, ai rivestimenti ed alle decorazioni (Chiarelli 2004).
Per frequenze fino a 50 Hz, si ritiene che la velocità di vibrazione della componente prevalente non debba superare il valore di 1, 3 e 8 mm/sec sulle fondamenta degli edifici rispettivamente appartenenti alla I, II, e III classe e che il valore della velocità risultante non debba, parimenti, superare i 3, 5, 10 mm/sec.
Superando detti limiti, in maniera sistematica, sorgono sicuramente problemi alle strutture seppure di livello minore.
Fasi di esecuzione
- Perforazione
Prima dell’esecuzione della volata, la piattaforma di perforazione esegue i fori – prededeterminati in fase di predisposizione del piano di brillamento – sul fronte di scavo del tunnel. Più solida è la roccia, più esplosivi sono necessari.
Una macchina chiamata jumbo viene utilizzato per praticare i fori nella parete rocciosa. La macchina ha solitamente tre bracci di perforazione (ma ne esistono di più grandi con un numero di bracchi superiore a tre) e una cabina operatore che manovra la macchina stessa. La macchina può praticare fori con lunghezza variabile da 2 a 6 metri.
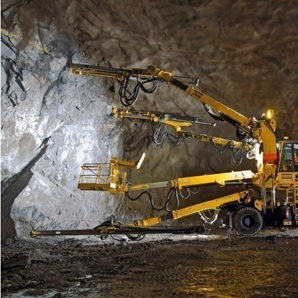
I primi set sono fori diritti (taglio parallelo) situati attorno al bordo della faccia di scavo (limite della sezione di scavo) e al centro. Un secondo set (taglio a V) è inclinato verso il centro. Questi permettono alla roccia di essere spazzata via dal fronte di scavo del tunnel durante la volata.
- Caricamento e brillamento
Successivamente alla realizzazione dei fori, questi vengono riempiti (saturazione) con dell’esplosivo e collegati a dei detonatori. I detonatori sono collegati ai dispositivi esplosivi (linea di tiro) e i singoli dispositivi esplosivi sono collegati tra loro (circuito di brillamento). I fori sono fatti saltare in una sequenza corretta, dal centro verso l’esterno, uno dopo l’altro. Sebbene possano essere innescate più di 100 esplosioni, una dopo l’altra, la blast sequence si completa in pochi secondi. I dispositivi non devono esplodere allo stesso tempo, ma piuttosto uno dopo l’altro a intervalli specifici. Solo quando si è certi che nessuno è rimasto nell’area di pericolo, l’esplosione può essere innescata dalla macchina di brillamento.
I tempi di esplosione tra le cariche sono distanziate di pochi millisecondi. La tecnica del frazionamento della volata consiste nel far esplodere per prima le cariche poste al centro del fronte di scavo o del nucleo roccioso e, successivamente, quelle poste verso l’esterno del contorno di scavo. La prima esplosione ha lo scopo di distendere il nucleo roccioso prima dell’esplosione delle restanti cariche. In aggiunta, la prima esplosione crea una superfice di distacco al contorno che agisce, sotto certi aspetti, da schermo alle onde d’urto provocate dal grosso delle volate. Così procedendo aumenta anche la capacità di frantumazione dell’esplosivo ottenendo materiali di risulta di dimensioni ridotte.
- Ventilazione
L’esplosione provoca, oltre alla frantumazione della roccia, un’enorme quantità di polvere che si mescola con i gas generati dall’esplosione.
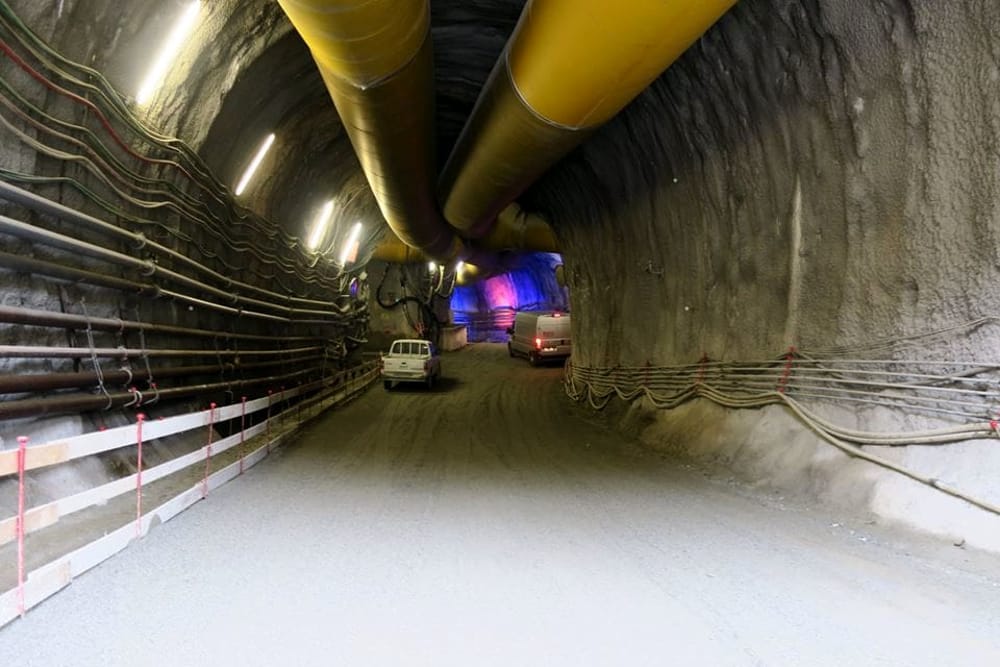
Affinché si possano riprendere le attività di disgaggio e smarino del materiale frantumato, l’aria carica di polvere e gas deve essere rimossa dal tunnel immettendone altra di pulita e fresca.Questo viene fatto attraverso i sistemi di canalizzazione dell’aria, lunghi tubi di acciaio o di plastica, che sono collegati in volta del tunnel e immettono aria pulita sul fronte di scavo. Ciò provoca una differenza di pressione localizzata e l’aria sporca insieme ai gas viene spinta verso l’uscita del tunnel. Per limitare la formazione di polvere durante il brillamento, quando possibile, dei getti d’acqua vengono indirizzati e spruzzati sul fronte di scavo in modo da abbattere le polveri.
- Smarino
Dopo che i pezzi di roccia sciolti sono stati rimossi dal fronte di scavo, il materiale o macerie viene portato fuori dal tunnel attraverso autocarri o cassoni installati su rotaie e trasportato dal sito di scavo alla discarica. Se di qualità della roccia è idonea allo scopo, essa può essere ulteriormente frantumata e ridotta alla pezzatura di impiego per il confezionamento del calcestruzzo che verrà impiegato poi per la formazione del rivestimento definitivo del tunnel e per tutte le altre opere in cui è previsto l’utilizzo di calcestruzzo.
- Rivestimento temporaneo e definitivo
Finite le operazioni di smarino, un rivestimento temporaneo generalmente costituito da calcestruzzo proiettato (spritz-beton) a rapida presa, è adoperato per stabilizzare le pareti e consentire un collegamento privo di cavità alla roccia proteggendo anche gli operatori da eventuali distacchi di roccia. A seconda del tipo di roccia, è possibile implementare una varietà di misure di fissaggio: rete metallica, centine, bulloni, chiodi che possono essere spinti nella roccia. Per la messa in opera di bulloni e/o chiodi è utilizzato un jumbo per praticare i fori. La distanza e la profondità di fissaggio tra i bulloni e/o chiodi è determinata dai geologi e/o dagli ingegneri che progettano il rivestimento temporaneo di stabilizzazione.
In presenza di rocce di scarsa resistenza meccanica e con uno stato fessurativo importante, potrebbe essere necessario mettere in opera archi in acciaio per sostenere le pareti e la volta del tunnel (centinatura). In altre situazioni, una rete d’acciaio può essere fissata alle pareti e al tetto per evitare che altri materiali sfusi cadano sui lavoratori sottostanti.
- Mappatura geologica
Quando il tunnel è stato posto in sicurezza ed il fronte di scavo è liberamente accessibile, i geologi effettuano una mappatura della roccia. Questo allo scopo di determinare il tipo di roccia presente, la giacitura, lo stato fessurativo, viene misurato l’angolo di incidenza e la direzione di incidenza delle strutture rocciose, si individuano eventuali pieghe, la presenza di piani di scorrimento e/o faglie mappate già in fase preliminare ed esecutiva di progettazione del tunnel.
Vengono scrupolosamente rilevate e documentate le caratteristiche meccaniche della roccia, la reazione della massa rocciosa al processo di scavo e l’eventuale infiltrazione di acqua di montagna. Il rapporto di mappatura creato è di fondamentale importanza per la progettazione e la messa in opera degli interventi di stabilizzazione del tunnel.
- Progettazione delle perforazioni
Il modello di perforazione assicura la distribuzione dell’esplosivo nella roccia e, di conseguenza, il risultato a seguito del brillamento dell’esplosivo. Diversi fattori devono essere presi in considerazione durante la progettazione della perforazione: perforabilità e effetti dell’esplosione sulla roccia, tipo di esplosivo da impiegare, limiti di vibrazione e requisiti di precisione.
Ogni sito ha le sue caratteristiche quindi anche i modelli di perforazione sono specifici per ogni sito e per tipo di roccia da abbattere.
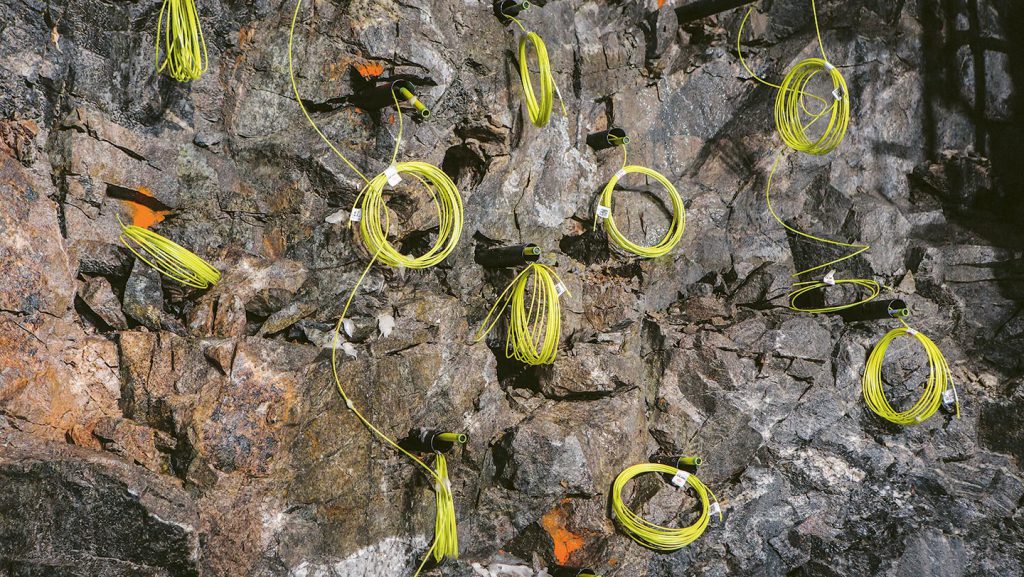
In generale, la progettazione del modello di perforazione nel tunnelling si basa sui seguenti fattori:
- Dimensioni della sezione del tunnel;
- Geometria del tunnel;
- Dimensione del foro di caricamento dell’esplosivo;
- Requisiti di qualità finali;
- Condizioni geologiche e meccaniche delle rocce;
- Disponibilità di esplosivi e mezzi di detonazione;
- Venute d’acqua preesistenti o causate dall’esplosione;
- Limitazioni alle vibrazioni;
- Attrezzature per la perforazione.
A seconda delle condizioni del sito, tutti o alcuni dei suddetti fattori sono considerati importanti per la progettazione del modello di perforazione del tunnel. Per ogni sito di costruzione e per ogni tunnel, in genere si dispone di diverse varianti dei modelli di perforazione (da un minimo di 5 ad un massimo di 10 modelli) per tenere conto delle mutevoli condizioni geomorfologiche e meccaniche delle rocce che si incontrano in fase di avanzamento dello scavo. Quando si progetta un modello di perforazione in galleria, l’obiettivo principale è garantire il numero ottimale di fori posizionati correttamente e accuratamente eseguiti. Ciò aiuta a garantire una saturazione ottimale del foro con l’esplosivo ed un brillamento di successo, oltre a creare pareti e calotta del tunnel accuratamente sagomati e lisci. Un modello di perforazione ottimizzato in questo modo è anche il più economico ed efficiente.
Conclusioni
L’abbattimento con esplosivo è un mezzo a tutt’oggi insostituibile e che molto probabilmente continuerà, anche in futuro, a rappresentare un metodo efficace e competitivo per scavare molte gallerie in rocce resistenti.
Questo metodo, tuttavia, lascia aperti due temi di discussione: la regolarità nella profilatura dello scavo e le vibrazioni indotte dallo sparo mine.
Una profilatura corretta ha positivi risvolti in termini tecnici, economici e di sicurezza: si riduce drasticamente il disgaggio, la possibilità di crolli fuori sagoma, il disturbo della massa rocciosa oltre il profilo di scavo, il consumo di calcestruzzo proiettato. La necessità di eseguire i fori di contorno divergenti per mantenere la sagoma, porta a fuori sagoma tecnici, che non possono essere eliminati, di entità dipendente dalla lunghezza della volata.
A prescindere da quelli tecnici, è necessario limitare il più possibile il fuori sagoma che derivano dalle condizioni geomeccaniche dell’ammasso in cui si scava. Questo è reso parzialmente possibile dalla riduzione della lunghezza di scavo al fronte e soprattutto dall’adozione di schemi di tiro controllato.
I parametri di base per il tiro controllato sono:
- il diametro dei fori di profilatura (normalmente 51/32mm);
- la distanza tra di essi (40÷90cm);
- la distanza tra fori di profilatura e l’ultima fila esterna dei fori di produzione (50÷100cm);
- il diametro della cartuccia di esplosivo (17÷25mm);
- la densità lineare di carica (0.2÷0.5kg/m).
Per la profilatura si utilizzano generalmente delle micce detonanti. Attualmente, l’esplosivo più utilizzato è di tipo ad emulsione pompata al posto delle cartucce. È necessario evidenziare che i migliori risultati potranno aversi solamente dopo un’accurata sperimentazione in sito.
Il problema della trasmissione delle vibrazioni indotte dallo sparo mine invece, è estremamente complesso per la presenza di molteplici fattori che intervengono nella generazione delle vibrazioni.
Per l’identificazione della propagazione sismica dei terreni interessati dallo scavo al fine di valutare i potenziali effetti vibratori indotti in superficie dal brillamento di cariche esplosive, in fase di avvio dei lavori, è necessario prevedere un piano di misura delle vibrazioni indotte, in galleria ed in superficie, mediante l’esecuzione di brillamenti controllati di alcune volate di prova.
In particolare occorre verificare in quale modo le caratteristiche geomorfologiche del sito (formazione rocciosa e coperture, stato di fratturazione della roccia, presenza di discontinuità strutturali ecc.) possano influenzare la propagazione delle onde elastiche, prodotte dagli scavi, dal sottosuolo alla superficie ed alla sicurezza delle strutture potenzialmente interferite. Tutto ciò avrà come scopo quello di individuare una legge di sito per la previsione del valore massimo di velocità di vibrazione originato dal brillamento delle cariche d’esplosivo.
Bibliografia [1]. M. Chiarelli – “L’Arte del costruire gallerie” – Editrice | Uni Service, Trento, 2009 ISBN: 978-88-6178-323-2 [2]. M. Chiarelli – “Le vibrazioni degli edifici indotte dalle ferrovie sotterranee” – “Strade & Autostrade” n°44, EDI-CEM Srl – MI [3]. M. Chiarelli – “Tecniche avanzate di scavo in sotterraneo mediante TBM, Microtunnelling e Horizontal Directional Drilling” – “INGENIO” n°17, Imready Srl – RSM [4]. M. Chiarelli – “La costruzione di gallerie in ambiente urbano” – “INGENIO” n° 28 e dossier di Geotecnica del 14 Novembre 2014, Imready Srl – RSM [5]. M. Chiarelli – “Infilaggi di rinforzo del terreno in galleria” – “Strade & Autostrade” n°131, EDI-CEM Srl – MI [6]. M. Chiarelli – “La ventilazione meccanica connessa alla sicurezza delle gallerie stradali” – “INGENIO web” del 15 Aprile 2016, Imready Srl – RSM |